線切割放電加工機是一種特種檢測儀器,在多個工程領域有著廣泛的應用。其通過向電極(通常是金屬絲)施加電壓,使其與工件相互靠近,從而破壞兩者之間的絕緣性,引發放電現象來進行加工的方法。在加工過程中,金屬絲與工件之間的空間被加工液充分填充,當兩者之間的距離足夠近時,電流會像閃電一樣從電極流向工件,產生劇烈的放電現象和大量的熱量。這種放電現象會持續進行,直至工件被切割開來。加工過程中產生的廢料會被加工液排出,同時電極與工件之間的絕緣性也會逐漸恢復。
1、操作前準備
設備檢查:確認設備接地良好,各部件連接牢固,無松動或損壞現象。檢查電極絲的安裝是否正確,余量是否滿足加工需求,并檢查其是否有破損或纏繞等情況。同時,查看加工液的液位、比電阻值是否正常,確保加工液循環系統暢通無阻。
工件準備:根據加工要求,選擇合適的工件材料,并將其表面清理干凈,去除油污、雜質等。使用合適的工裝夾具將工件固定在機床工作臺上,確保工件的位置準確、牢固,且不會在加工過程中發生位移或振動。
參數設置:根據工件的材料、厚度、形狀以及加工精度要求等,在設備控制系統中設置相應的加工參數,如脈沖電壓、脈沖電流、脈沖寬度、脈沖間隔、進給速度、放電間隙等。這些參數的合理選擇直接影響加工效率和質量。
2、加工操作過程
開機與尋原點:打開設備電源開關,啟動機床。在控制系統中選擇“尋機械原點”功能,使機床的坐標軸自動回到初始位置,建立準確的坐標系,以確保加工精度。
導入加工軌跡:根據工件的加工要求,使用專業的編程軟件繪制加工軌跡,并將其生成的代碼或圖形文件導入到線切割放電加工機的控制系統中。常見的編程軟件有AutoCAD等,可通過特定的接口或數據傳輸方式將軌跡信息傳輸給設備。
定位與對刀:移動機床的工作臺和電極絲,使電極絲與工件的起始加工位置對齊??梢酝ㄟ^手動操作或使用自動對刀功能來完成這一步驟,確保電極絲與工件之間的距離準確無誤,避免因定位不準確而導致的加工誤差或斷絲等問題。
開始加工:設置好加工參數和加工軌跡后,先啟動冷卻系統,使加工液充分循環,然后開啟放電加工功能。在加工過程中,密切觀察設備的運行狀態,包括電極絲的張力、放電狀態、加工液的流量和溫度等,確保加工過程穩定進行。同時,注意聆聽設備的運行聲音,如有異常應及時停機檢查。
實時監控與調整:通過設備的顯示屏或控制系統軟件,實時監測加工過程中的各項參數和數據,如坐標位置、放電間隙、加工速度等。根據實際加工情況,適時調整加工參數,以優化加工效果。例如,如果發現加工速度過快導致放電不穩定,可以適當降低進給速度;如果加工精度不符合要求,可以調整放電間隙或脈沖參數等。
3、加工完成后操作
關機:加工完成后,先將進給速度降至z低,關閉放電加工功能,待電極絲停止運動后,再關閉冷卻系統和設備的電源開關。按照設備的關機流程,逐步退出操作系統,確保設備安全關機。
工件處理:將加工好的工件從工作臺上卸下,清除工件表面的附著物和加工屑,檢查工件的加工質量是否符合要求。如有必要,可以進行進一步的清洗、打磨或其他后處理工序。
設備清潔與維護:清理機床工作臺上的切屑、油污等雜物,保持工作區域的整潔。檢查電極絲的使用情況,如剩余長度、磨損程度等,及時更換電極絲。對設備進行全面的檢查和維護,包括潤滑部件、檢查電氣系統、校準坐標等,確保設備處于良好的運行狀態,為下一次加工做好準備。
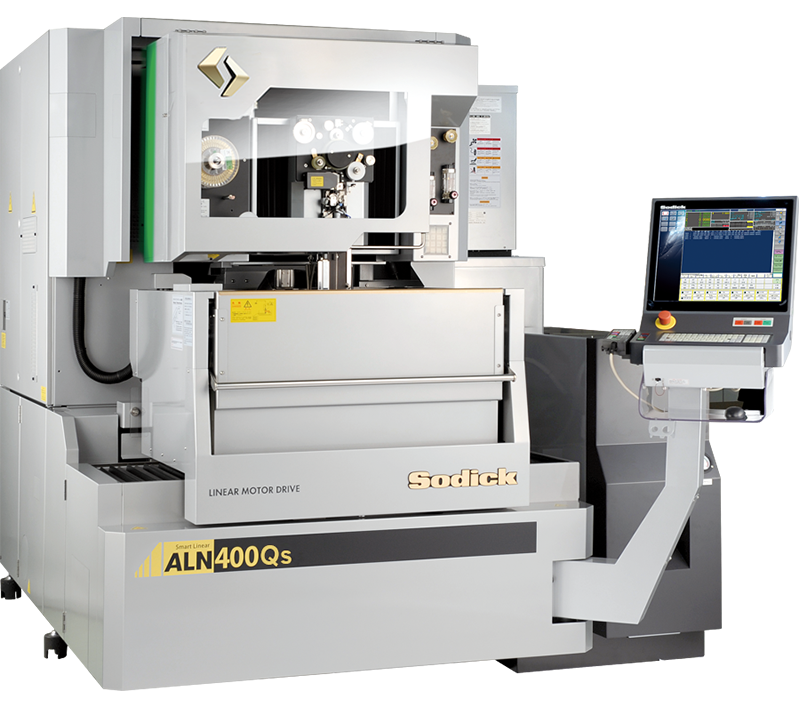